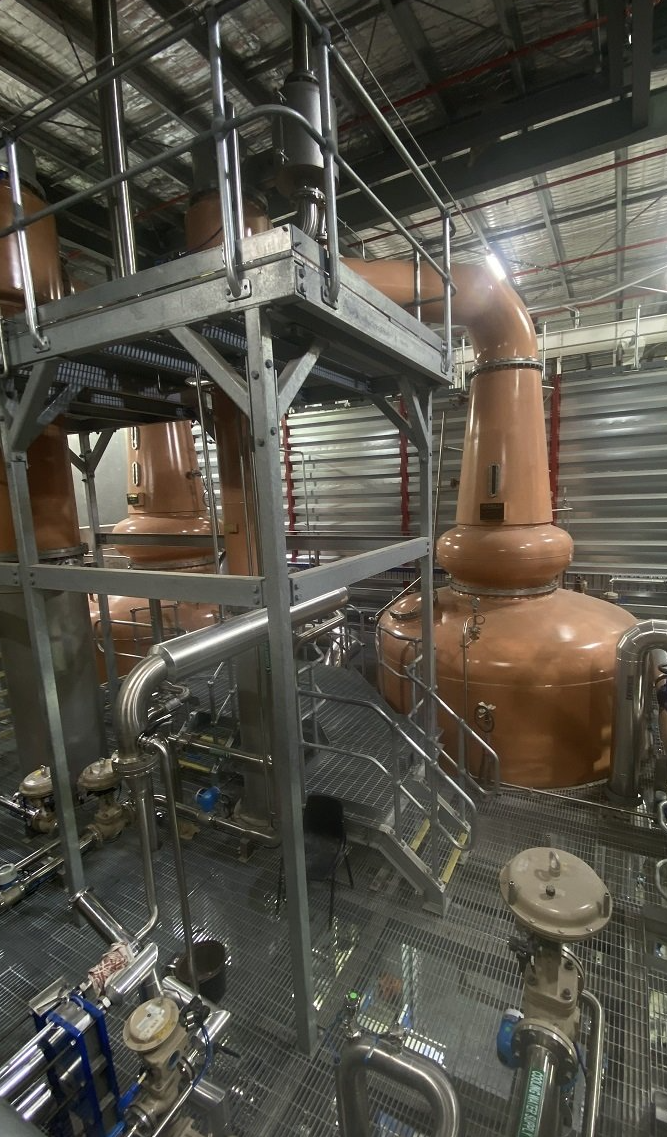
Client - Archie Rose
Project – Distillery installation
Cost – $5+ Million
Duration – 18 months, completed early 2020
Workforce – Total at peak of project – 58 personnel
Scope
Founded in 2014 and located in Rosebery, Sydney – just a few kilometres south of the Sydney CBD – Archie Rose Distilling Co. is proudly Australia’s most highly awarded distillery producing a diverse range of whiskies, gins, vodkas and rums. The new site features energy efficient brewing and distilling technology, some of which is the first of its kind in Australia. The distillery was custom built to accommodate Archie Rose’s unique production processes, including its six-malt single malt mash bill, extensive use of specialty roasted malts, malted rye and individually distilled gin botanicals.
TRIPLENINE was engaged by Archie Rose to provide layout finalisation & design detailing, fabrication, installation and commissioning support of all process and services systems based on supplied design specifications
Working in tandem with the team at Archie Rose and the process engineers, as well as vendors and suppliers from around the world, Triplenine helped infuse a national landmark with 21st-century infrastructure that is setting new standards for sustainable production.
Systems include the following:
- Mash house
- Fermentaion
- Whiskey & Gin stills
- Distillate
- Spirit handling
- Cask Filling & Disgorging
- IBC station
- Tanker bay
- CIP set
- Process water
- Heating and cooling systems
- Compressed air
- Waste handling
-
Equiment installation
ButtonA total of 108 vessels ranging in size from 2KL to 70KL, 81 pumps, 18 heat exchangers were installed.
TRIPLENINE were responsible for offloading, positioning and levelling of all equipment
-
Structural steel design & installation
ButtonApprox 120ton of structural steel support structures and walkways were installed as part of the project
-
Piping installation
ButtonA total of 10,500 mts of process and services piping was installed, the majority of the piping installed was 316L SS tube with Carbon steel being specified for all high and low pressure steam distribution.
To monitor and control the system safely 551 instruments and 1435 manual and actuated valves were installed
Take a walk through the model
Model was developed using Autodesk plant 3D, Tekla structures, Inventor & navisworks
"Making dreams become reality"
Construction challenges
Each construction project poses unique challenges and this project was no exception, together with all stake holder and through good management TRIPLENINE were able to successfully deliver an outstanding facility that we are proud put our name against.
Project photo gallery
Just some random photo's taken throughout the project
Leadership in Safety
A total of 74,000 man hours were undertaken to complete this project with zero lost time incidents
999 is continuously developing a strong safety culture