SERVICES
ORBITAL TUBE AND PIPE WELDING
From our humble beginnings as a two-man operation, Triplenine has continually updated and expanded to include highly skilled personnel and an extensive inventory of orbital welding equipment.
We pride ourselves on being a market leader in this space and have built a track record of providing significant quality and value for its customers.
Hygienic & UHP Process Piping Systems
By utilising the next generation orbital welding equipment, our fully trained operators are able to cover tube sizes ranging from 0.25 inches to 4.0 inches for closed head welding the most common tube sizes in this type of industries. Triplenine utilise state of the art tube preparation tools and testing equipment ensure a quality oriented fabrication process. Proven quality management procedures and well trained tradespeople close the cycle of project delivery.
Expect :
• Orbital welding and installation procedures to ASME-BPE Standards
• Arc Machines Inc.® EXPERIENCED and trained orbital machine operators
• Certified welding operators to ASME standard
• Comprehensive weld documentation packages
• High quality QA packages, IQ verification packages
• Dedicated project management team
• BIM (Autodesk®REVIT® PLANT3D) capable
Why Orbital Welding?
Weld Repeatability, Consistency, and Efficiency
Orbital Welding was first introduced in the late 1960’s as a way to reduce the weight of hydraulic and fuel systems on commercial aircraft.In the Pharmaceutical Industry: In the late 1970’s orbital welding began to be used for Pharmaceutical water systems as a way to eliminate any Contamination or areas where water may be retained for possible bacteria Growth…as can happen with manual welding.
In the Semiconductor Industry: In the early 1980’s with the explosion in semiconductors orbital welding was introduced as a method to improve Yields through improved gas purity and leak integrity.
There are many reasons for using orbital welding equipment. The ability to make high quality, consistent welds repeatedly,
at a speed close to the maximum weld speed, offer many benefits to the user:
Exotic materials & heavy wall, High pressure piping utilising orbital welding
Tripleine nine have extensive experience with wire feed orbital welding
Uses Of Orbital Welding In The Aerospace Industry
Orbital Welding is now used in the Aerospace Industry on many systems and components such as: Titanium Fuel Lines, Hydraulic Lines and Components and Aluminium Ducting
Uses Of Orbital Welding In The Aerospace Industry
Orbital Welding is now used throughout the Pharmaceutical Industry for: CIP Skids, WFI Loops, Diaphragm Valves, Diaphragm Pressure Gauges and Clean Steam Systems
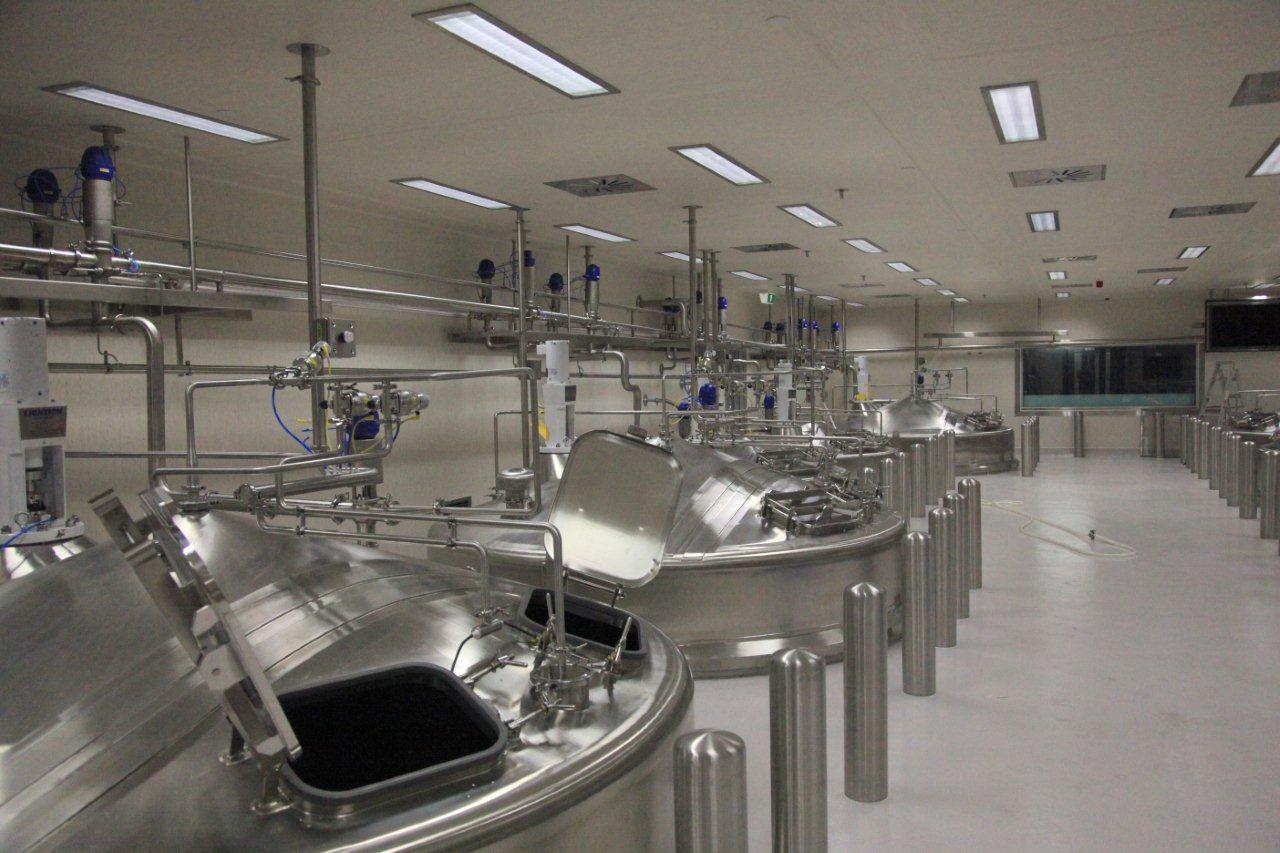
Uses for Semiconductor Gas Delivery Systems
Material chemistry and heat, Weld procedure parameters, Tungsten geometry and eccentricity when it orbits, Tube cleanliness, Purge gas quality and quantity, Ambient conditions and Input power
Uses for Semiconductor Gas Delivery Systems
Orbital Welding is now used in the Aerospace Industry on many systems and components such as: Titanium Fuel Lines, Hydraulic Lines and Components and Aluminium Ducting
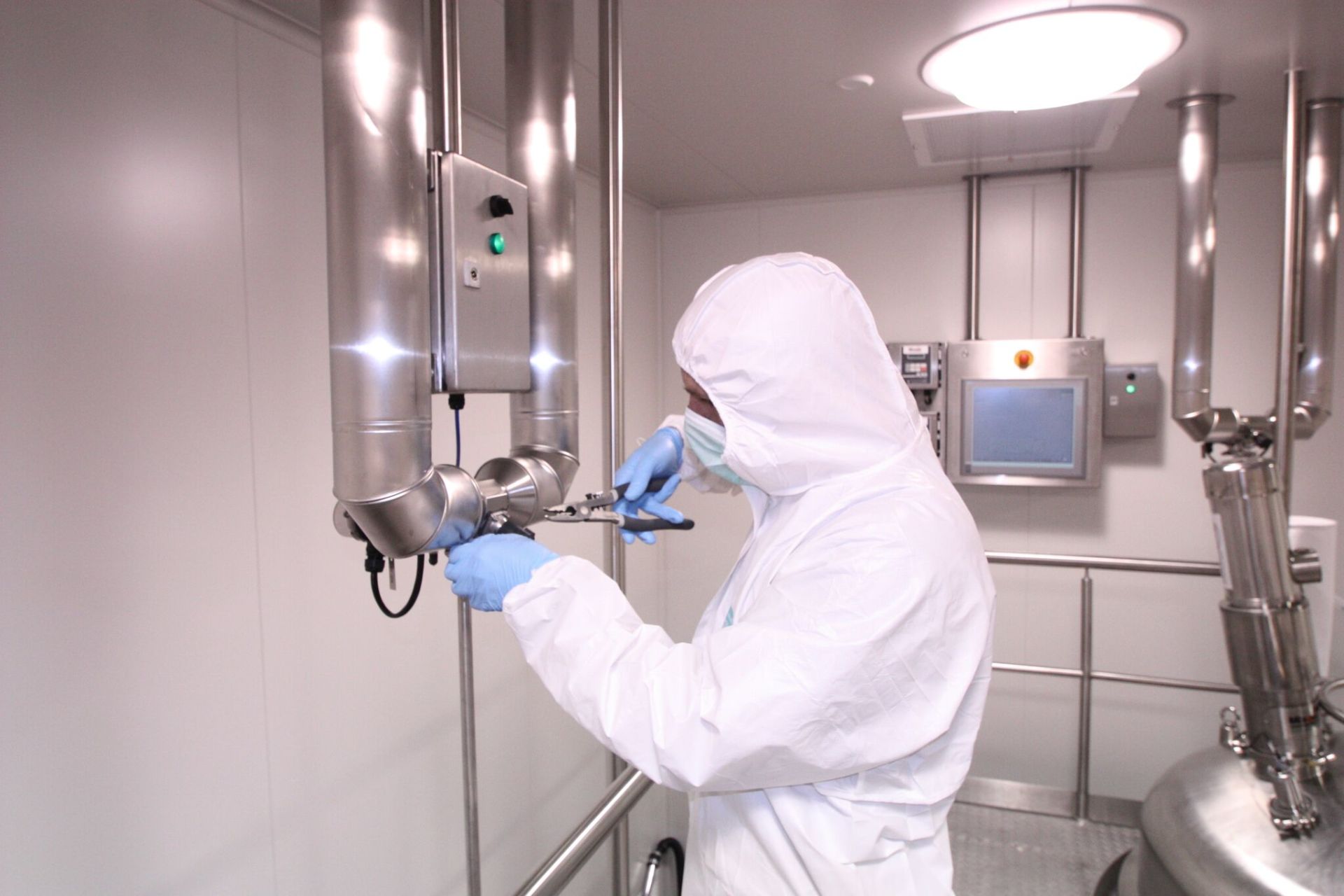
Uses for Semiconductor Gas Delivery Systems
- Extremely repeatable welds, Smooth and even tube bore and smaller
- Heat affected zone (HAZ)
- Elimination of defects including porosity and cracking
Uses for Semiconductor Gas Delivery Systems
Material chemistry and heat, Weld procedure parameters, Tungsten geometry and eccentricity when it orbits, Tube cleanliness, Purge gas quality and quantity, Ambient conditions and Input power
CONSISTANCY
Once a weld program has been established, an orbital welding system can repeatedly perform the same weld hundreds of times, eliminating the normal variability, inconsistencies, errors, and defects of manual welding.